Cycle Counting Inventory
Poor inventory accuracy within your walls results in losing customers
People have favorites. You hear, “what’s your favorite food?” and something comes to mind. If you’re with a group of people, the conversation will evolve, and someone is bound to have a favorite that another doesn’t particularly care for but will eat and someone in the group won’t eat that because of a scarred childhood memory. It’s the same way with your products. You have best sellers that are your staples, those that people will use on occasion, all the way down to discontinued items, and special items you ordered in once and will probably never use again but are holding on to. Your customers’ “favorite items” need to be well stocked to keep operations running smoothly and your customers happy. This gets challenging if your inventory is inaccurate. For example, if your Warehouse Management System (WMS) says you have 325 pieces, but in reality, you have 100 pieces, you may not be able to fill an order when needed, or even worse, lose a client.
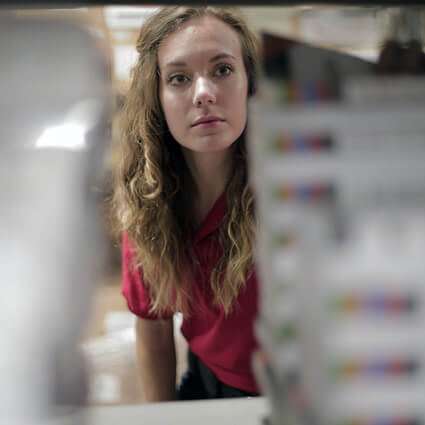
We're Here to Help
Monarch knows that having a proactive cycle count program can ensure inventory accuracy. We are ready to assist your team to meet cycle counting goals or help develop a cycle counting program from scratch to work in your existing operational schedule. During peak times, operational focus shifts to getting orders out the door. In these times, Monarch can assist with cycle counting support within established processes.
The Process
- Listen. Tell us the concerns you have when it comes to maintaining your inventory accuracy within the 4 walls. Do you have any unique products that always need to be in stock but might not turnover very quickly? Do you have seasonality in your operation? What is your historical count pace within your current cycle count program?
- Analyze. To find your customers’ “favorites” we’ll want to have a minimum of 6 months’ worth of your shipping history.
- Prioritize. With that data we’ll run an ABC priority which helps categorize the products, determining how often each specific product should be counted. The goal is to completely cycle count through all items at least once within a years’ time, more often for your fast-moving products.
- Plan. With your guidance we will complete your cycle counting program by fine tuning details such as how often you want the staff to complete the counts (daily, weekly, monthly). We’ll look at the specifics, such as your operation schedule. What is the best time to perform the counts?
- Automate. Most WMS programs provide for the ability to track cycle counts with auditing capabilities that will trigger recounts and verification. Where processes are established it will be important for cycle counters supporting the effort to learn this process. For new programs being set up, it will be necessary to configure the cycle counting program within the WMS.
- Document. In the case of a new process, standard operating procedures (SOPs) will need to be developed. SOPs should follow a consistent format with clear and concise steps to establish consistency across the cycle counting program.
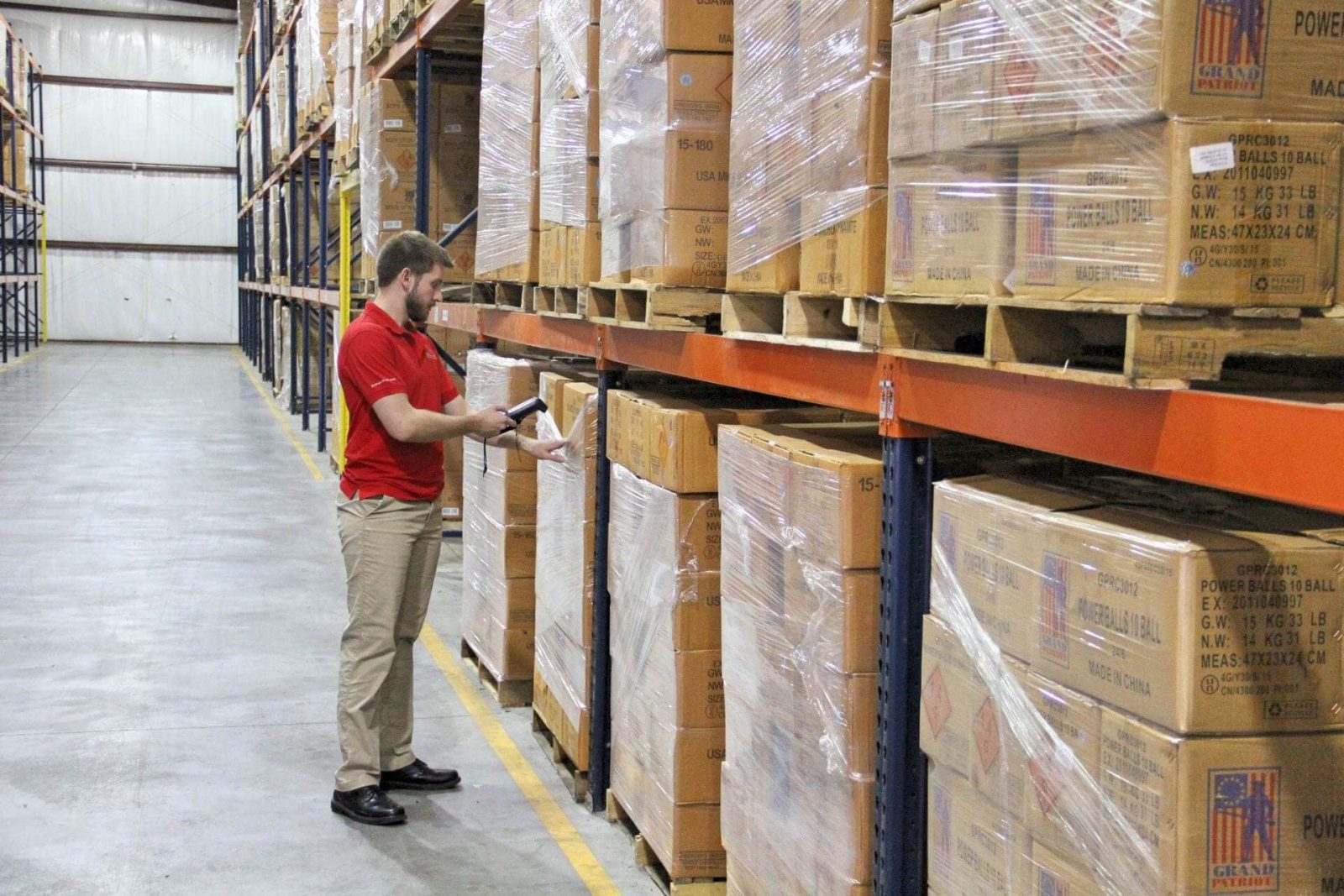
Blind Counts
We always utilize a blind count methodology, meaning the person in charge of counting a specific item does not have access to the quantities in the WMS. We’ve found this requires them to actually investigate each item and perform an actual count instead of just verifying that what they see physically matches what is on the handheld. A blind count requires due diligence, analysis, and counting versus giving the option of saying “well the system says 200 and yeah that looks like 200 to me”.
Warehouse Inventory Services We Provide
Your Inventory Service Questions Answered
Get answers to your most common questions from Monarch
How familiar are you with cycle counting?
We have operational experience performing cycle counts in both manufacturing and distribution facilities ranging from under 100K sq ft to over 1M sq ft. We have helped establish new cycle counting programs and worked within existing cycle counting programs to simply help an organization get caught up.
How fast can you ramp up to support a cycle counting initiative?
Once we understand the scope and have our teams in place for your project, the process will move very quickly. We have experience working with an array of warehouse management systems and our teams have experience working within these processes. The skill level of our team means that we are quick studies and will pick up on how your system works in no time.
How well do you adapt to the culture of your customers?
We have established a culture of teamwork within Monarch. We value the character attributes of hungry, humble, and people smart. If on-time arrival, exceeding performance targets, and asking questions as we learn your operation are important to you, then our teams will integrate well. Our teamwork oriented mindset within our people has shown them to be very adaptable to a variety of different cultures.